为了提高生产率,在加工零件的同一台机床上对该零件进行测量似乎合情合理。毕竟,机床上一般都有测量所需的轴系和足够的工作空间,并通常配备有触发式机床測头。然而,在机测量的效果往往并不尽如人意。为什么高精度的机床测头测量后仍然需要在专用三坐标测量机(CMM)上进行呢?
与金属切削机床一样,CMM的制造精度也会受到经济可行性的限制。然而,与机床不同的是,
CMM通过对整个工作空间进行基于计算机的误差补偿(即空间误差补偿),可以实现更高的测量精度。
例如,一台CMM制造完成后,要用激光干涉仪精确测出其误差图,对直线度、垂直度、直线定位精度和角度误差的误差函数进行测量并制成误差表。
由于CMM的零部件几何尺寸可视为恒定不变,因此可以利用测量软件对这些误差进行合并和修正。
虽然空间误差补偿技术已在CMM上普遍采用,但对加工机床来说,对滚珠丝杠误差以外的其他误差项进行修正的情况并不多见。
那么,对机床进行空间误差补偿为何难度更大呢?由于机床的零部件几何尺寸并非恒定不变,因此使其在至少四个重要方面与CMM明显不同。
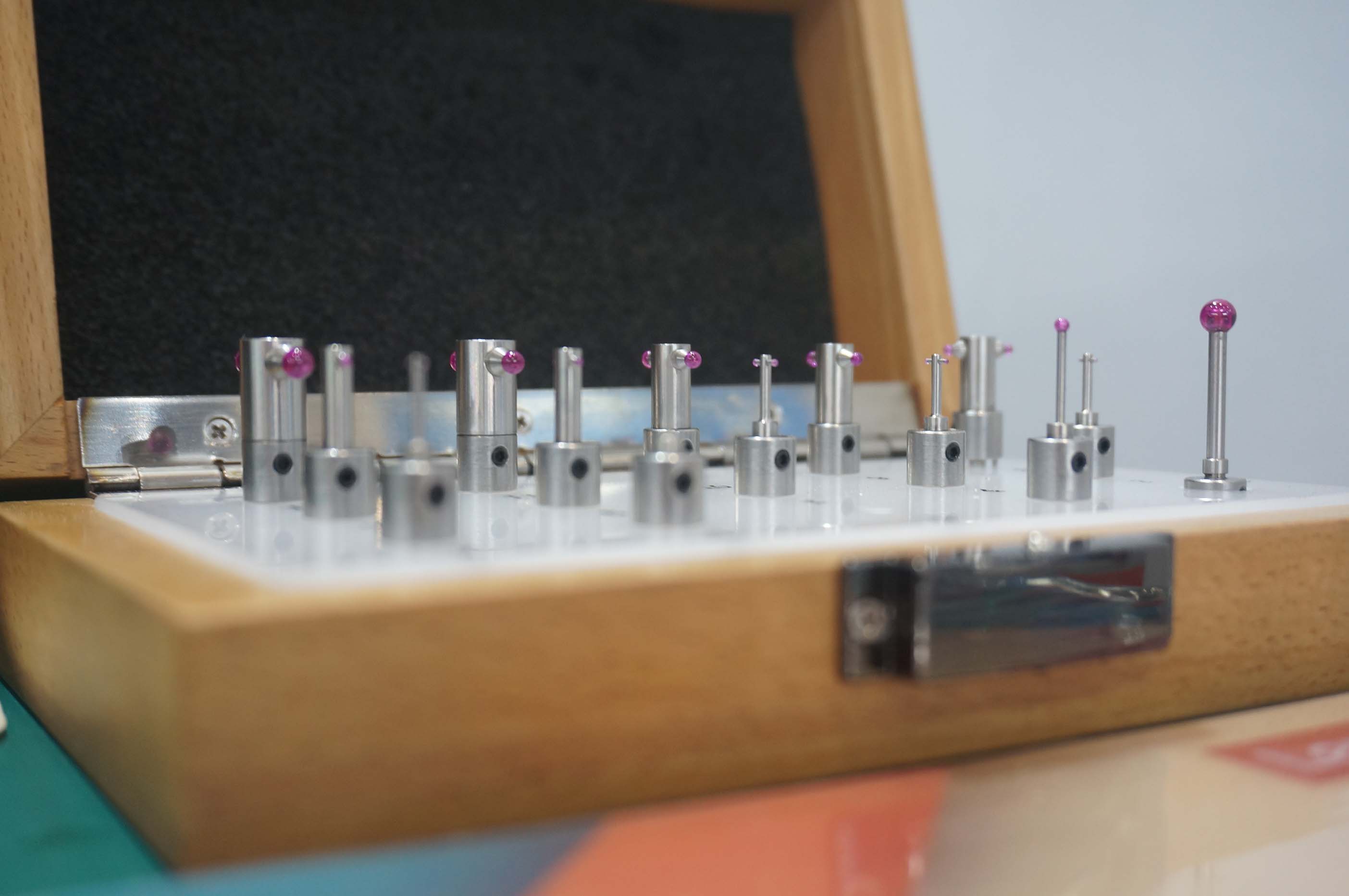
CMM通常都放置在严格控制温度的工作环境中。计量室的温度通常保持在20℃(规定的尺寸测量标准温度),一般都配备有空调装置、隔温门和专门的温控系统,以保证温度的波动范围很小(通常为零点几度)。在对工件进行测量之前,需要预先"等温"一使被测工件的温度与计量温度完全相同。
而机床的加工环境往往对温度缺乏严格的控制。阳光可能会从窗户照进室内,通向室外的门可能是敞开的。虽然加工车间通常都比较热,但只有少数车间装有空调。不断变化的环境温度会改变机床的几何尺寸。就像机床有振动模式一样,它也有热模式,但这种热模式的时间常数比较长,通常为几小时或几天。
CMM本身没有较大的热源。虽然CMM也有用于驱动轴系的伺服电机,但其所需的功率很小。CMM的轴系通常采用气浮轴承,因此产生的摩擦热很低。而机床有驱动电机、预加载轴系和主轴,并且会吸收切削热和喷溅上温度较低的冷却液。由于所加工的零件不同,这些热源的开启和关闭很难预测。机床上的热源会激发其热模式,其结果是,机床零部件的位置始终在移动。以一台主轴安装在垂直立柱前面的机床为例。当主轴首先启动时,产生的热量主要包含在主轴中,远离立柱。此时主轴位置向+Y方向移动。在当天晚些时候,即使该主轴仍以相同的速度在相同的负荷下运转,它产生的热量开始传入立柱中(但是在立柱的正面而不是背面)。此时立柱发生变形,并开始向后倾斜,使主轴向-Y方向移动。正如更常见的那样,当机床主轴启动和停止、加速和减速时,由发热引起的误差都会变得难以预测。
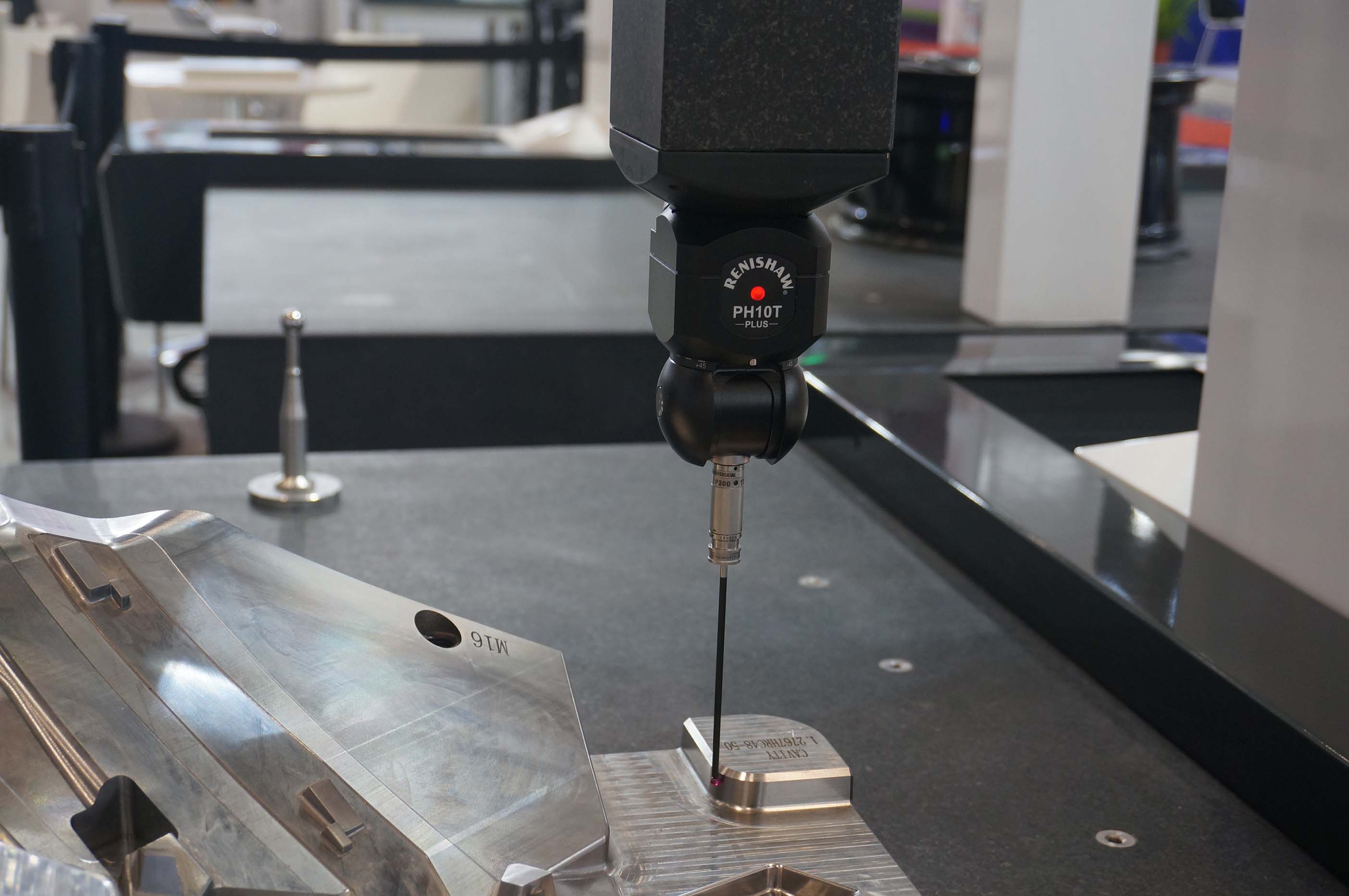
CMM并不需要知道每一点的位置坐标,而是需要在测头"点击"采样时精确地确定所在的位置。因此,CMM的驱动系统和导轨必须非常灵活。而机床必须处于某些特定的加工位置,并要对抗很大的切削力在这些位置保持不动。因此,机床的驱动系统和导轨必须具有很好的刚性。为了消除空程,机床的轴系必须预加载荷,而这样会产生较大的摩擦。机床的回程误差可能是一个相当严重的问题,而CMM的回程误差则要小得多。与CMM不同的是,为了与刀具的切削动作保持一致,机床的轴系必须以规定的速度移动(且往往是高速移动)。
CMM通常不会承受较大的测量负荷。测头与被测工件之间的接触力可能仅为几毫牛顿。因此,CMM在测量过程中的变形通常很小,而且一般局限于工件重量(作用于CMM的工件重量测量时不会发生变化)以及运动部件质心不断变化的影响。机床则要承受很大的加工负荷。切削力可能很容易就会高达数百磅。切削会产生很大的主轴扭矩,而快速移动的重载轴系则会产生惯性负荷。
由于这些原因,对机床进行空间误差补偿相当困难。当然,这并不意味着机床不能用于测量,而是表明,与用机床测量相比,用CMM测量的精度要高得多-至少目前还是如此。